by Wayne Graham
This article was published in the spring 2025 issue of our newsletter.
I have been writing this column about unique solutions to difficult problems since 2008. I didn’t want these great ideas to get buried over the 17 years, so here is a “best of” compilation of how operators have solved problems, saved money, and made life at their second home—the treatment plant—a little easier.
Use Old Chlorine Ventilation for Chemical Odors
Many treatment facilities handle chemical room odors by venting their chemical storage tanks into ductwork originally designed for gas chlorine evacuation. These existing ventilation systems usually have a blower that comes on when the room’s lighting is turned on. A good work practice would be to turn on the light/blower a few minutes prior to entering the room.
This idea is especially useful when dealing with sodium bisulfite odors. Take care not to run the blower too long in the winter as sodium bisulfite will crystalize around 45°F.
I have seen this in Hardwick, Barton, and Orleans, but I am sure that others have thought of it as well.
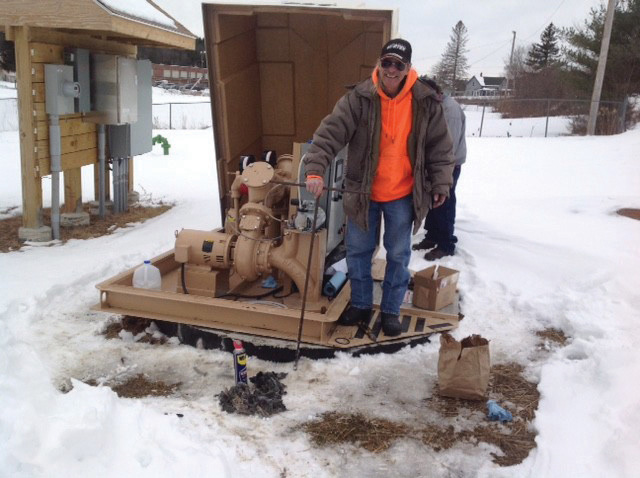
Buddy Ball uses a curb stop screw auger tool to remove a blockage.
Use Tools to Clear Clogged Pumps
Ever encounter a pump so bound up with debris and “flushable” wipes that you couldn’t remove the tangled mess? The ever-inventive Buddy Ball, superintendent Lunenburg Fire District 2, found a quick solution to this issue by using a curb stop screw auger tool to remove the blockage. This saved him from having to dismantle the pump.
As a safety note, don’t reach into a pump with your hands because of the risk of hypodermic needles and razor blades. Take Buddy’s cue and use tools or pliers to remove such debris. You might want to invest in puncture-resistant gloves as well when working on pumps or handing screenings.
Protect Electrical Panels from Cold
Outdoor electrical panels/enclosures may have issues with cold temperatures and moisture. Operators at the Shelburne WWTFs installed a dehumidifier designed for a gun safe that circulates warm, dry air throughout the panels on a continual basis. This keeps the door panel seals from freezing, the switch gear from sticking, and prevents moisture from building up!
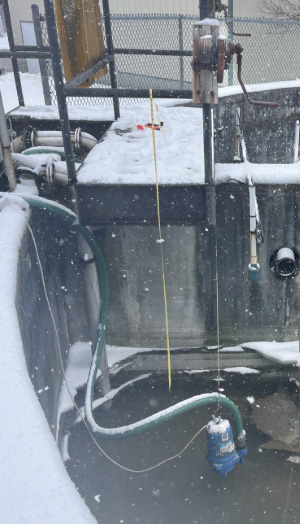
Decant pump (blue, bottom right) attached to a winch (top right).
Use a Winch to Raise and Lower a Decant Pump
The crew at the West Rutland WWTF installed a very simple and very effective sludge storage tank decant pump on a winch system. This allows them to raise and lower the pump as the sludge levels fluctuate so the pump is always at the right level to remove the liquid on top. This design is extremely effective and even self-draining for cold weather use.
Remove Sludge while Lagoons are in Operation
The Village of Jeffersonville has a two-cell aerated lagoon facility. It used to be quite a balancing act to dewater and remove sludge from one lagoon, while the other held all of the flow without discharging a partially treated effluent! This was difficult, labor intensive, and expensive.
After extensive research, the Village purchased a sludge dredge system and geotextile tubes for sludge dewatering. The biggest benefit of this system is that the lagoons can stay in normal operation while sludge is removed from the bottom. The operators have been very happy with the process.

Impeller coated with ceramic protectant.
Extend the Life of Impellers
Do you have pump impellers and volutes that experience heavy wear? After receiving training from a local machine shop, St. Johnsbury operators coat the inside of volutes and entire impellers with a ceramic protectant. They have been doing this for years and see a huge difference in pump component longevity.
Two Tricks for Bar Racks
Trevor Welch at the Jeffersonville WWTF had issues with surface aerator performance. The aerator props were very prone to getting tangled with debris from the influent that passed through the coarse bar rack, so he added fine bar screen downstream. This addition has made the aerators much more reliable.
Speaking of manually raked bar racks, ever try to rake one in freezing temperatures? It results in quite a frozen mess. Try splashing influent on the racks, drainage platform, and the rake itself. A very thin layer of ice forms and keeps the screenings from sticking to the metal. As any operator knows, handling screenings from bar racks and screens is not a fun part of our jobs (in fact, I tell new operators in the Basic Wastewater Course that if they only learn one thing from me, it’s to keep your mouth closed when raking a bar rack!)
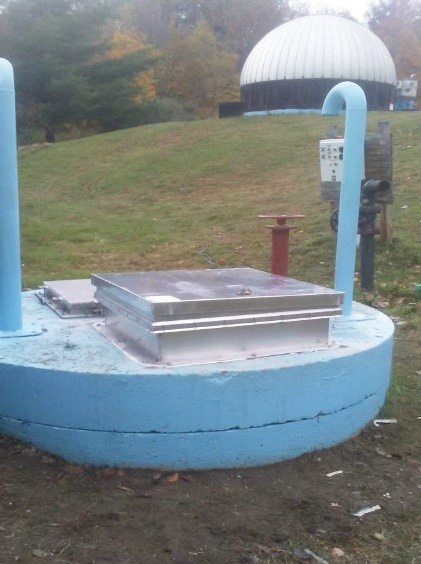
The Sugarbush Utilities pump station.
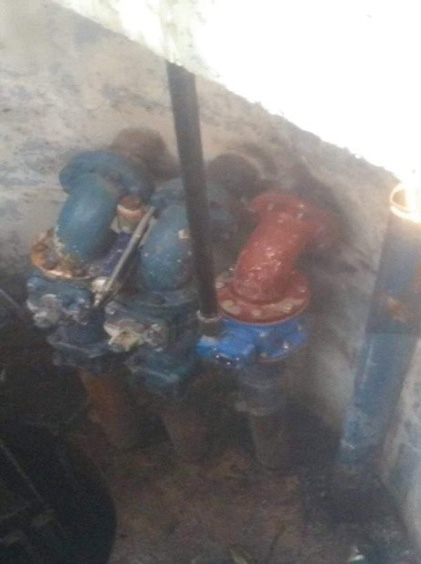
The retrofitted valve handle (black) allows for safer operation from ground level.
Vertical Valve to Avoid Confined Space Entry
When complying with safety regulations, sometimes engineered solutions (aka work-arounds) are warranted. The Sugarbush Utilities staff at Mountain Wastewater Treatment, Inc. did just that by hiring Laramie Water Resources to do some interesting retrofits so they could avoid repeated confined space entries. Phil Laramie’s crew cored a hole in the concrete pump station wet well and installed a vertically operated valve. This allows the operators to open and close the valve from above using a valve key. The operators no longer have to enter this confined space to turn the valve.
Prevent Effluent Discharge during Power Outages
The Danville WWTF uses UV disinfection, so if the power went out and the UV lights shut off, the effluent wouldn’t get disinfected. They solved their power failure concerns by installing automatic valves on the effluent line. When the power goes out, these valves immediately close, which stops effluent discharge. This ensures that effluent that hasn’t been disinfected won’t be discharged. The facility does not need a generator for short power outages that are less than 24 hours. This method works because Danville is a small lagoon plant, but other facilities may experience overflows if their effluent discharge is closed for an extended period.
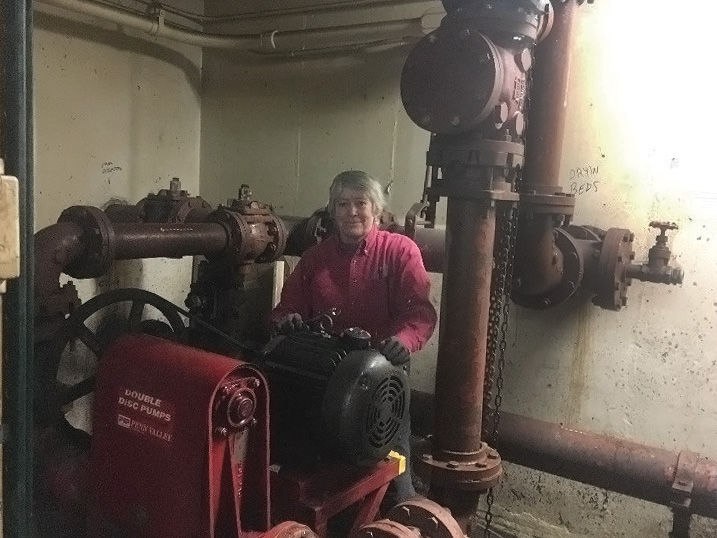
Elizabeth Walker installing the pump.
Retrofit an Old Pump
Sometimes Vermont Rural Water staff even dabble in Yankee Ingenuity. The North Troy wastewater plant was in desperate need of a return activated sludge pump. They were in the middle of an engineering review and not in a position to purchase a new pump. Now-retired VRWA wastewater specialist Elizabeth Walker and I repurposed a Penn Valley pump from another facility. With some piping modifications and assistance from plant staff, it was operating flawlessly in no time!
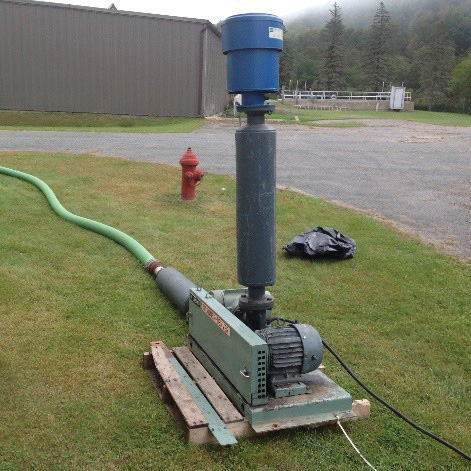
The portable blower assembly.
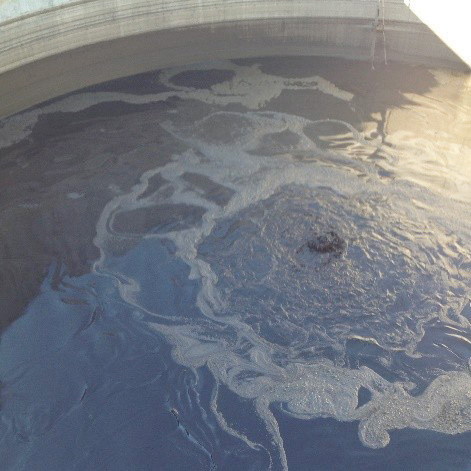
A holding tank being mixed by the blower.
If Mixers Won’t Work, Use a Blower Instead
Another cheap and very effective fix from the operators in St. Johnsbury was finding a way to keep their 1.2 MG sludge holding tank mixed when the sludge level was lower than the mixers. The staff set up a portable blower on a skid and now blow air into the bottom of the tank cone through a sludge line.
Asymmetrical run time
This is an idea that I stole 38 years ago from operators at my first wastewater job in West Lebanon, NH. If you have duplicate pieces of equipment, especially duplex or triplex units, don’t run them for equal amounts of time.
Contrary to what most equipment suppliers will tell you, alternating equipment to maintain equal run hours is not a good idea. The reason for this is that if you have two units of the same blower, pump, motor, etc. and you run them equally, then chances are when one of them wears out, the second unit is in similarly poor condition. This leaves you with the dilemma of having one unit broken or under repair and your back up unit is also at risk of failing.
An example of a better rotation is to run your lead unit six days a week and your backup unit one day per week. When the lead unit is ready for rebuild, your backup unit will still be in good shape.
Granted, there will be exceptions to this such as warranty issues, when you may want to max out equipment run time, or equipment that needs to be operated or exercised daily.
A good practice that can be used facility-wide is to exercise your backup units while exercising your generator. This will keep your electrical demand charges down.
If you have interesting ideas that you want to share, send them to me to be included in future articles. I also encourage you to tour other facilities and share ideas; you will find that networking with other operators can be very beneficial. Several organizations can help; VTWARN, GMWEA, VT Watershed Management Division, and of course, Vermont Rural Water.
Stay safe out there, we need you!